In modern electronics manufacturing, where nanoscale circuitry and sensitive components are prevalent, electrostatic discharge (ESD) poses a significant threat. Often undetectable to humans but devastating at the microelectronic level, ESD compromises device reliability, increases production costs, and damages brand credibility. As components shrink below 5nm and IoT devices expand, the industry faces a paradox: while miniaturization drives innovation, it also exponentially increases vulnerability to ESD.
What does ESD stand for in process control?
From the Basic Knowledge of ESD, we know that how ESD is generated. While static electricity mostly may feel harmless in daily life, its industrial consequences are far more severe. Though undetectable to human senses, ESD poses a critical risk in electronics production. A single static transfer can either instantly destroy components or create hidden flaws that bypass standard quality checks. These latent defects often surface later as unexplained field failures, leading to costly warranty claims, safety risks, and lasting damage to brand reputation.
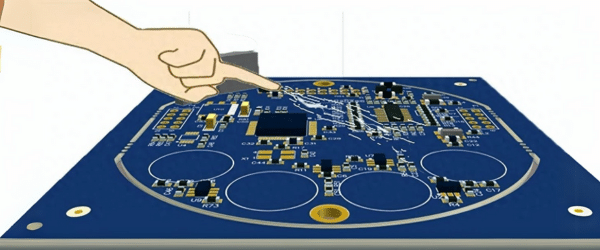
As a result, a comprehensive ESD control program—including Eionization systems, ESD Control Area, humidity control and ongoing training for employees and more—are crucial for ensuring eletronics product reliability .
Two failure modes in dlectronic components caused by ESD
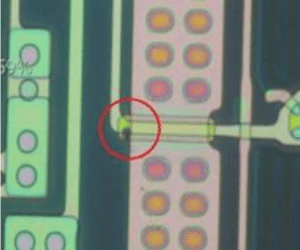
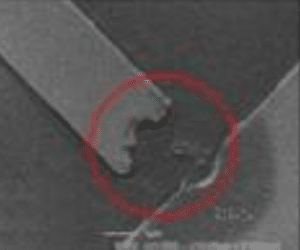
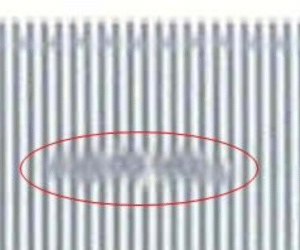
1. Catastrophic Failure
- Complete loss of functionality due to severe degradation of electrical parameters
- Represents ~10% of ESD-induced component failures
2. Latent Defects
- Components initially meet specifications but exhibit:
- Significantly reduced operational lifespan
- Compromised reliability
- Potential for sudden failure under subsequent stress
- Accounts for ~90% of ESD-related damage
This latent failure mode poses greater risks as compromised components may pass initial quality checks but cause field failures in end products.
ESD-Induced failure mechanisms in electronics manufacturing
- Misalignment During Assembly
Static fields can displace micro-components during placement, causing tombstoning or weak solder joints that escape detection until later testing phases. - Charge Buildup in Equipment
SMT machinery’s conductive parts accumulate static, risking latent damage to semiconductors if not neutralized via grounding or ionization. - Contamination Acceleration
Charged surfaces attract dust 100x faster, creating conductive paths that trigger short circuits or signal interference. - Parasitic Component Adhesion
Static causes parts to cling to packaging or tools, risking physical damage and residual charges that skew test results.
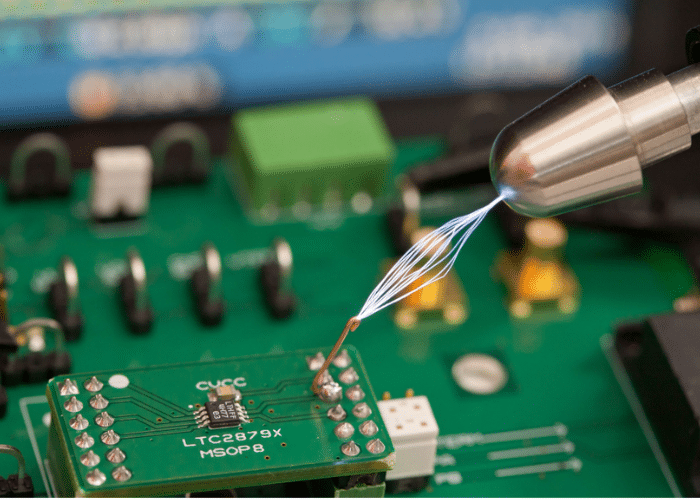
ESD-related incidents in electronics manufacturing
ESD causes an estimated $5 billion to $9 billion in annual losses to the global electronics manufacturing industry, according to a 2021 report by the ESDA. These losses stem from damaged components, production delays, and costly recalls. Below are notable real-world incidents highlighting ESD’s severe financial and operational impacts
1. AMD Processor Failures (1994)
Company: Advanced Micro Devices (AMD)
Incident: ESD during handling damaged thousands of K5 processors during production, causing latent defects and field failures.
Loss: Estimated $12M in replacements and reputational damage.
Source: ESD Association Case Study
2. Automotive ECU Recall (2018)
Company: Major European Auto Manufacturer
Incident: ESD during assembly corrupted firmware in 150,000 engine control units (ECUs), causing random shutdowns.
Loss: $47M in recalls and production halts.
Source: Industry report by IATF 16949 auditors (Page 22).
3. Tesla Model 3 Touchscreen Failures (2020)
Company: Tesla
Incident: ESD-sensitive touchscreen components degraded prematurely due to insufficient factory grounding.
Loss: $135M recall (NHTSA Campaign 21V035000).
Source: NHTSA Recall Report (Search “21V035000”).