Dans la fabrication électronique moderne, où les circuits à l'échelle nanométrique et les composants sensibles sont fréquents, les décharges électrostatiques (ESD) constituent une menace importante. Souvent indétectable par l'homme mais dévastatrice au niveau microélectronique, la décharge électrostatique compromet la fiabilité des appareils, augmente les coûts de production et nuit à la crédibilité de la marque. Alors que les composants se réduisent en dessous de 5 nm et que les appareils IoT se développent, l'industrie est confrontée à un paradoxe : alors que la miniaturisation stimule l'innovation, elle augmente aussi de manière exponentielle la vulnérabilité aux décharges électrostatiques.
Que signifie ESD dans le contrôle des processus ?
A partir de la Connaissance de base de l'ESDNous savons maintenant comment l'électricité statique est générée. Si l'électricité statique peut sembler inoffensive dans la vie quotidienne, ses conséquences industrielles sont bien plus graves. Bien qu'indétectables par les sens humains, les décharges électrostatiques représentent un risque critique dans la production électronique. Un seul transfert d'électricité statique peut soit détruire instantanément des composants, soit créer des défauts cachés qui échappent aux contrôles de qualité standard. Ces défauts latents apparaissent souvent plus tard sous la forme de défaillances inexpliquées sur le terrain, entraînant des réclamations coûteuses au titre de la garantie, des risques pour la sécurité et une atteinte durable à la réputation de la marque.
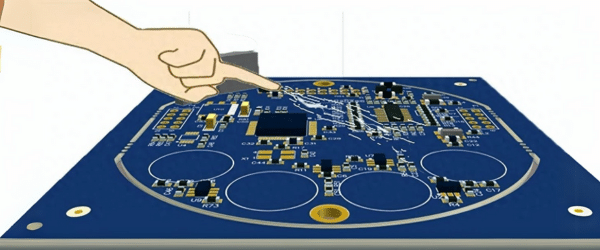
En conséquence, un rapport complet sur l'état d'avancement de la mise en œuvre de la Programme de contrôle ESDm-y compris les systèmes d'ionisation, Zone de contrôle ESDLe contrôle de l'humidité et l'évaluation de la qualité de l'air en cours training pour emsalariés sont essentiels pour garantir la fiabilité des produits électroniques.
Deux modes de défaillance des composants électroniques causés par les décharges électrostatiques (ESD)
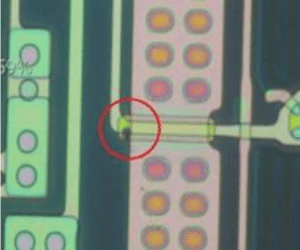
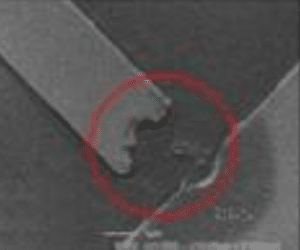
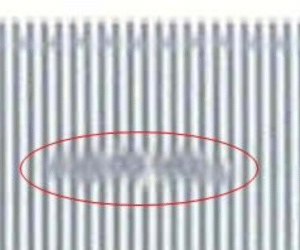
1. Défaillance catastrophique
- Perte totale de fonctionnalité en raison d'une dégradation importante des paramètres électriques
- Représente ~10% des défaillances de composants induites par les décharges électrostatiques (ESD)
2. Défauts latents
- Les composants sont initialement conformes aux spécifications, mais ils présentent des défauts :
- Durée de vie opérationnelle considérablement réduite
- Fiabilité compromise
- Risque de défaillance soudaine sous l'effet d'une contrainte ultérieure
- Est responsable de ~90% des dommages liés aux décharges électrostatiques (ESD)
Ce mode de défaillance latent présente des risques plus importants, car des composants compromis peuvent passer les contrôles de qualité initiaux mais provoquer des défaillances sur le terrain dans les produits finis.
Mécanismes de défaillance induits par les décharges électrostatiques (ESD) dans la fabrication de produits électroniques
- Désalignement lors de l'assemblage
Les champs statiques peuvent déplacer les microcomposants lors de la mise en place, ce qui entraîne la formation de pierres tombales ou de joints de soudure fragiles qui ne sont détectés qu'au cours des phases de test ultérieures. - Accumulation de charges dans l'équipement
Les pièces conductrices des machines SMT accumulent l'électricité statique, ce qui risque d'endommager latéralement les semi-conducteurs si elle n'est pas neutralisée par la mise à la terre ou l'ionisation. - Accélération de la contamination
Les surfaces chargées attirent la poussière 100 fois plus vite, créant des chemins conducteurs qui déclenchent des courts-circuits ou des interférences de signaux. - Composant parasitaire Adhésion
L'électricité statique fait que les pièces s'accrochent à l'emballage ou aux outils, ce qui risque d'entraîner des dommages physiques et des charges résiduelles qui faussent les résultats des tests.
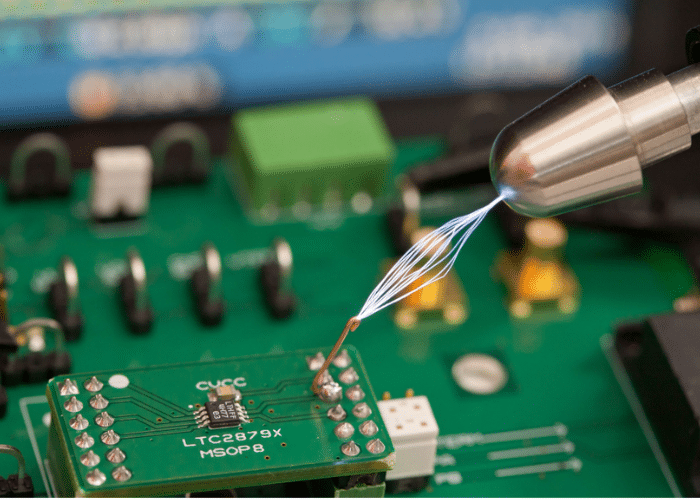
Incidents liés aux décharges électrostatiques dans la fabrication de produits électroniques
L'ESD est à l'origine de pertes annuelles estimées entre $5 et $9 milliards pour l'industrie mondiale de la fabrication de produits électroniques, selon une étude réalisée par l'Institut européen de recherche sur les technologies de l'information et de la communication (IESIC). Rapport 2021 de l'AESD. Ces pertes résultent de composants endommagés, de retards de production et de rappels coûteux. Voici quelques incidents réels notables qui mettent en évidence les graves incidences financières et opérationnelles de l'ESD
1. Défaillances des processeurs AMD (1994)
Entreprise: Advanced Micro Devices (AMD)
Incident: Les décharges électrostatiques au cours de la manipulation ont endommagé des milliers de processeurs K5 pendant la production, provoquant des défauts latents et des défaillances sur le terrain.
Perte: Estimation de $12M en remplacements et atteinte à la réputation.
Source: Étude de cas de l'association ESD
2. Rappel de calculateurs automobiles (2018)
Entreprise: Grand constructeur automobile européen
Incident: Des décharges électrostatiques au cours de l'assemblage ont corrompu le micrologiciel de 150 000 unités de contrôle du moteur (ECU), provoquant des arrêts aléatoires.
Perte: $47M dans le cadre de rappels et d'arrêts de production.
Source: Rapport de l'industrie par les auditeurs de l'IATF 16949 (page 22).
3. Défaillances de l'écran tactile de la Tesla Model 3 (2020)
Entreprise: Tesla
Incident: Les composants de l'écran tactile sensibles aux décharges électrostatiques se sont dégradés prématurément en raison d'une mise à la terre insuffisante en usine.
Perte: Rappel $135M (Campagne NHTSA 21V035000).
Source: Rapport de rappel de la NHTSA (Recherche "21V035000").