Nella moderna produzione elettronica, dove prevalgono circuiti su scala nanometrica e componenti sensibili, le scariche elettrostatiche (ESD) rappresentano una minaccia significativa. Spesso impercettibili per l'uomo ma devastanti a livello microelettronico, le ESD compromettono l'affidabilità dei dispositivi, aumentano i costi di produzione e danneggiano la credibilità del marchio. Con la riduzione dei componenti al di sotto dei 5 nm e l'espansione dei dispositivi IoT, il settore si trova ad affrontare un paradosso: se da un lato la miniaturizzazione spinge l'innovazione, dall'altro aumenta esponenzialmente la vulnerabilità alle ESD.
Cosa significa ESD nel controllo di processo?
Dal Conoscenza di base dell'ESDsappiamo come si generano le scariche elettrostatiche. Mentre l'elettricità statica può sembrare innocua nella vita quotidiana, le sue conseguenze industriali sono molto più gravi. Anche se non rilevabile dai sensi umani, l'ESD rappresenta un rischio critico nella produzione di elettronica. Un singolo trasferimento statico può distruggere istantaneamente i componenti o creare difetti nascosti che eludono i controlli di qualità standard. Questi difetti latenti spesso emergono in seguito come guasti inspiegabili sul campo, causando costose richieste di garanzia, rischi per la sicurezza e danni duraturi alla reputazione del marchio.
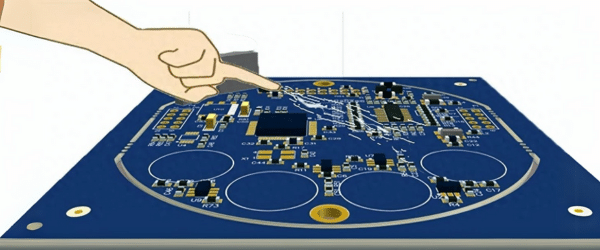
Di conseguenza, un'analisi completa Programma di controllo ESDm-compresi i sistemi di ionizzazione, Area di controllo ESD, controllo dell'umidità e in corso training per emdipendenti e altro ancora, sono fondamentali per garantire l'affidabilità dei prodotti elettronici.
Due modalità di guasto nei componenti elettronici causati da ESD
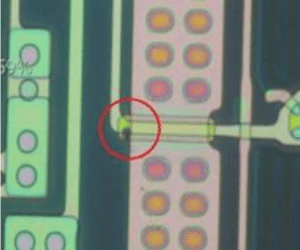
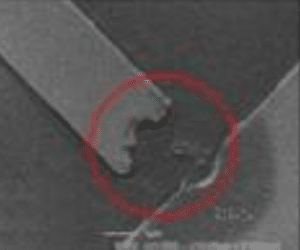
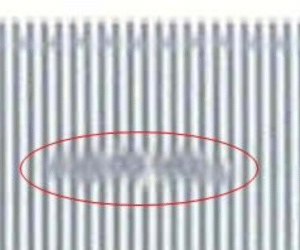
1. Fallimento catastrofico
- Perdita completa di funzionalità a causa di un grave degrado dei parametri elettrici
- Rappresenta ~10% di guasti di componenti indotti da ESD
2. Difetti latenti
- I componenti inizialmente soddisfano le specifiche, ma si manifestano:
- Durata di vita operativa significativamente ridotta
- Affidabilità compromessa
- Potenziale di cedimento improvviso in caso di sollecitazioni successive
- Responsabile di ~90% dei danni legati alle ESD
Questa modalità di guasto latente comporta rischi maggiori, in quanto i componenti compromessi possono superare i controlli di qualità iniziali ma causare guasti sul campo nei prodotti finali.
Meccanismi di guasto indotti da ESD nella produzione elettronica
- Disallineamento durante il montaggio
I campi statici possono spostare i microcomponenti durante il posizionamento, causando tombstoning o giunti di saldatura deboli che sfuggono al rilevamento fino alle successive fasi di test. - Accumulo di carica nelle apparecchiature
Le parti conduttive dei macchinari SMT accumulano cariche elettrostatiche, con il rischio di danni latenti ai semiconduttori se non vengono neutralizzate tramite messa a terra o ionizzazione. - Accelerazione della contaminazione
Le superfici cariche attirano la polvere 100 volte più velocemente, creando percorsi conduttivi che innescano cortocircuiti o interferenze di segnale. - Adesione dei componenti parassitari
La statica fa sì che i componenti si aggrappino all'imballaggio o agli strumenti, con il rischio di danni fisici e cariche residue che alterano i risultati dei test.
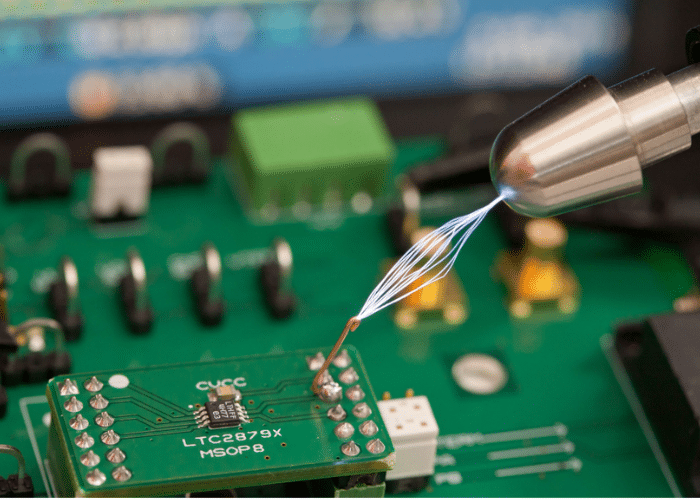
Incidenti legati alle ESD nella produzione elettronica
Secondo una stima di $5 miliardi - $9 miliardi di perdite annue per l'industria manifatturiera elettronica mondiale, l'ESD è causa di un'erosione del tessuto industriale. Relazione 2021 dell'ESDA. Queste perdite derivano da componenti danneggiati, ritardi di produzione e costosi richiami. Di seguito sono riportati alcuni episodi reali che evidenziano i gravi impatti finanziari e operativi delle ESD.
1. Guasti dei processori AMD (1994)
Azienda: Dispositivi micro avanzati (AMD)
Incidente: Le scariche elettrostatiche durante la manipolazione hanno danneggiato migliaia di processori K5 durante la produzione, causando difetti latenti e guasti sul campo.
Perdita: Stima di $12M in sostituzioni e danni alla reputazione.
Fonte: Studio di caso dell'Associazione ESD
2. Richiamo della centralina automobilistica (2018)
Azienda: Un grande produttore europeo di automobili
Incidente: Le scariche elettrostatiche durante l'assemblaggio hanno danneggiato il firmware di 150.000 unità di controllo del motore (ECU), causando spegnimenti casuali.
Perdita: $47M in richiami e interruzioni della produzione.
Fonte: Relazione di settore dei revisori IATF 16949 (Pagina 22).
3. Guasti al touchscreen della Tesla Model 3 (2020)
Azienda: Tesla
Incidente: I componenti del touchscreen sensibili alle scariche elettrostatiche si sono degradati prematuramente a causa di una messa a terra insufficiente.
Perdita: Richiamo $135M (campagna NHTSA 21V035000).
Fonte: Rapporto di richiamo NHTSA (Cercare "21V035000").